Blog
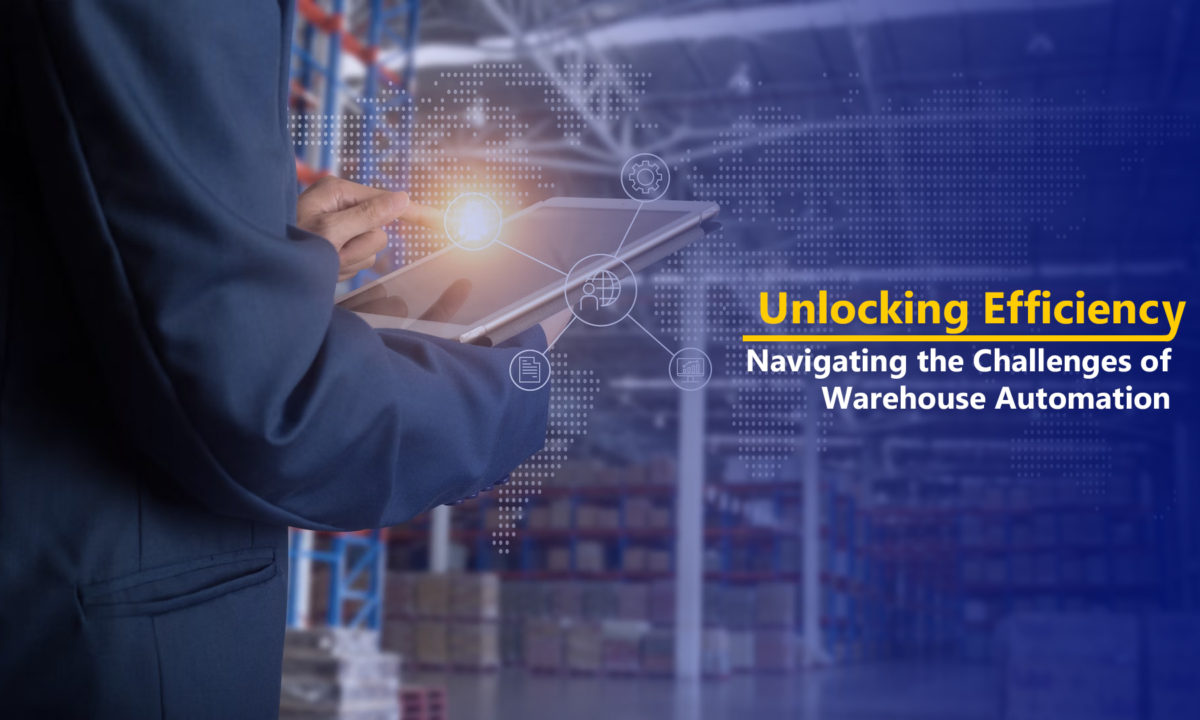
Challenges and Barriers in Adopting Warehouse Automation
As industries strive for increased efficiency and productivity, warehouse automation has emerged as a promising solution. Implementing automated technologies in warehouses can lead to streamlined operations, reduced human errors, and improved overall performance. However, despite its numerous benefits, the adoption of warehouse automation comes with its set of challenges and barriers. In this blog, we will explore some of the key obstacles and solutions that companies experience while automating their warehouses.
High Initial Investment and Return on Investment (ROI) Concerns
One of the primary hurdles in adopting warehouse automation is the upfront cost. Implementing automated systems, such as robotics, conveying, and sorting machines, can require capital investment. Many businesses, especially small and medium-sized enterprises (SMEs), may find it challenging to allocate the necessary funds to initiate the automation process.
For budgeting automation at the warehouses, buyers should look at the total cost of ownership (TCO) of the system. TCO refers to the overall cost associated with acquiring, operating, and maintaining an asset or investment over its entire lifecycle. Hence, while calculating the ROIs, both the initial investment and the ongoing costs are considered to get an accurate picture of the returns generated by the investment which could be less daunting.
Having said that, there are ways in which companies can enjoy the flavour of automation by taking smaller steps and opting for entry-level systems for the processes which are acting as bottlenecks, rather than opting for end-to-end automation in one go. For example, an e-commerce company can look at adopting a static or dynamic DWS profiler that will help them automate the GRN at the inbound, optimizing storage density, and efficient load planning at the outbound. These systems are designed to automatically capture barcodes, weights, and dimensions of items with high accuracies, eliminating human dependencies and human errors, eventually leading to more accurate data that can be utilized for correct billing reconciliation with courier partners and eventually reducing revenue loss.
Although automation promises increased productivity and efficiency, it could take some time to see a good return on investment. Companies must carefully evaluate the potential benefits of automation against the initial costs and ongoing expenses. Setting realistic expectations for ROI is essential to avoid disappointment and maintain commitment to the automation journey.
Integration with Existing Systems
Many warehouses already have established legacy systems and processes, including warehouse management software and inventory tracking tools. Integrating new automation technologies with these existing systems can be complex and time-consuming. Ensuring seamless communication and compatibility between different automated components and legacy software is a significant challenge for warehouse managers.
The warehouse owners should evaluate the competencies of the technology sellers for being able to provide in-house developed WCS software (acts as a bridge between customer’s software and their hardware), flexibility in the WCS in an as-is state, and if required, the ability of the automation provider to customize the WCS according to the customer’s WMS and order management systems.
The advantages of having an inhouse capability to make changes in the WCS software are multi-fold and provide flexibility in operations to warehouse owners with changing business needs.
Workforce Adaptation and Training
As automation becomes more prevalent in warehouses, it inevitably changes the nature of the workforce. Employees may feel anxious about job security and fear of being replaced by machines. Companies must address these concerns through transparent communication and retraining programs that empower employees to work alongside automated systems rather than being replaced by them. As it is said “Automation doesn’t replace people. It replaces professions”
Scalability and Flexibility
Warehouses often face fluctuating demands and seasonal peaks, making scalability and flexibility crucial. Implementing automation systems that can adapt to changing requirements can be challenging. Companies should look to invest in flexible automation solutions that can be easily reconfigured or expanded as needed.
Most of the legacy systems that solve warehouse automation needs are fixed in nature, such as conveyors, racking, traditional ASRS, etc., and the others that offer higher flexibility are available at a higher price point. To solve this challenge, companies can evaluate automation solutions that are modular in nature and can be scaled according to the growing business needs.
It is also important to evaluate the downtime required to implement the upgrade and the changes required to be done to the existing operating procedure to accommodate this upgrade. The companies should plan accordingly to ensure minimal business discontinuity time.
Maintenance and Downtime
Automated systems require regular maintenance to ensure smooth operations. Unplanned downtime can be costly, impacting productivity and disrupting supply chain operations. Having a well-structured maintenance plan and quick-response support team is essential to minimize downtime and keep automation systems running efficiently.
Companies should explore options for Annual and Comprehensive Maintenance Contracts (AMCs/CMCs) from the automation providers. Companies should be careful to calculate the overall maintenance cost of the system for the required time period. Generally, it is seen that the cost of a Comprehensive Maintenance Contract looks higher at the face of it, but when compared to the overall maintenance cost of the system throughout its life, opting for CMCs can prove to be much more cost-effective.
In addition to this, it is advised for the companies to maintain critical spares at the site that are easily accessible at the time of a breakdown/maintenance visit. This eliminates the lead time from ordering, manufacturing, and delivering a particular spare part, thereby exponentially reducing the system downtime.
Technological Complexity and Expertise
Warehouse automation involves complex technologies, such as artificial intelligence, machine learning, and robotics. To successfully implement and manage these systems, companies need skilled personnel with expertise in handling and troubleshooting advanced technologies.
While hiring and retaining such talent can be a challenge for many organizations, they can choose a technology provider that provides trained and qualified manpower on-site to maintain such systems.
Conclusion
Warehouse automation offers immense potential for improving operations, reducing costs, and enhancing customer satisfaction. However, adopting automation is a complex process that comes with its set of challenges and barriers. Overcoming these hurdles requires careful planning, investment, and a proactive approach to address the workforce and management’s concerns.
By understanding and tackling the challenges head-on, businesses can unlock the true potential of warehouse automation and position themselves for long-term success in the dynamic and competitive world of supply chain management. Embracing automation with a strategic outlook will lead to a more agile, efficient, and future-ready warehouse ecosystem.
For the latest updates, follow us on:
Facebook | LinkedIn | Instagram | Youtube