Blog
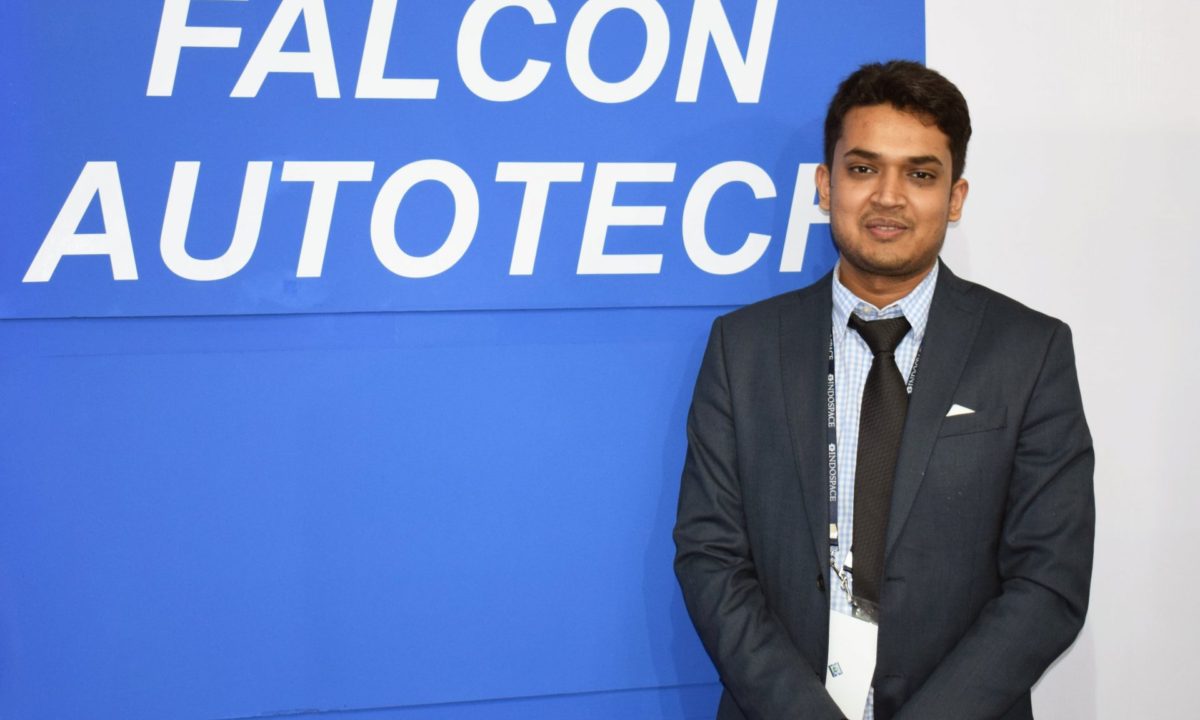
Warehouse automation in India ripe for explosion within ten years: Naman Jain, Falcon Autotech
Automation and the spurt in connectivity holds enormous potential to make sectors such as manufacturing and logistics resilient and efficient. Makeover of the warehouse, the crucial node in a supply chain between an enterprise and end-users, will make processes more seamless, transparent and customer-friendly. It will help enable better experiences.
Greater Noida based Falcon Autotech is among the pioneers in the transformation of the modern warehouse. It is one of the leading Indian warehouse automation companies with a global presence across sectors. The IPO-bound logistics firm Delhivery recently invested in it.
Falcon Autotech will continue its global expansion and deploy large-scale projects in India for some of the biggest companies this year. With solutions tailored to meet the requirements of retail markets, it operates across e-commerce, grocery, fashion, parcel, pharma, food/FMCG and spare part retail supply chains.
“In 2022, we expect to launch our goods to person 3D robotic shuttle system called NEO3D, which has been under development for four years. It will be a game-changer for the fulfilment market in India”, says Naman Jain, CEO, Falcon Autotech, in an exclusive interview with Geospatial World.
As the world wrangles with Covid-19 pandemic, one acute issue that has surfaced is supply chain disruption and the dire need of smarter supply lines that can weather shocks. What role can warehouse and logistics automation play in decoupling existing supply chains and making them more efficient, robust and resilient?
A significant impact of the pandemic on warehouses has been the lack of workforce – either due to local lockdowns, or restrictions on number of people allowed to work in a shift. This severely hampers a company’s ability to continue operations even at reduced volumes. This is where warehouse automation can play a pivotal role. We have consistently seen companies that have invested in it fare better compared to others.
Warehouse automation not only enhances the overall volume handling ability, but also ensures that work can be done with a reduced workforce. It has enabled our clients to continue their operations at sustainable volumes even with a fraction of workforce available.
How essential do you think is location intelligence and data-based analytics in warehouse automation, and going forward how do you see the sector shaping up with the exponential rise in data sharing and connectivity through 5G and AI?
The world of warehouse automation is totally different from what it used to be a decade back. Today customers demand ever-smarter systems that can leverage huge amount of data using advanced technologies such as Machine Learning and Deep Learning.
One example is Falcon’s DLIC engine that was introduced last year. The industry has faced a consistent challenge in automatically identifying a box shaped parcel from a non-box shaped parcel. No reliable technology was available in the market for this identification at high speed and accuracy.
When our clients approached us to find a solution to this problem, we looked at various options and ultimately used Deep Learning as the preferred solution. The results were promising and our clients are quite happy. This would not have been possible ten years ago. It is only due to the rapid advancements in AI that such use-cases have turned into a reality.
Today many companies are working on these advanced tools to come up with innovative solutions to real-world problems. For instance, Remote Virtual Commissioning is made possible by 5G, and predictive maintenance via AI/ML.
Industrial IoT is going to be a game-changer for manufacturing and logistics, but a key challenge is infrastructural readiness and bucking up for the transition ahead. What is your view on the immense transformative potential of Industrial IoT, and how willing companies are to adapt to it?
There’s no doubt that Industrial IoT is the future. With democratization of electronics and rapid advancements in 4G/5G rollouts, we are at the cusp of Industrial IoT revolution.
From real-time tracking of on-field equipment and the ability to take proactive actions, to monitoring energy generation and consumption of a building and controlling the energy spends with predefined custom rules, there are multiple applications. Automating multiple tasks that was deemed impossible earlier, is now a reality.
Companies are highly receptive to good ideas in this direction and a lot of pilot projects are underway. It’s only a matter of time before we see a boom in large-scale implementation of Industrial IoT in manufacturing and logistics, however, right implementation would be the key.
What do you think would be the future of warehouses in India, and what can be done to promote smart automation for myriad sectors?
India is a booming economy with rising consumption among the middle-income groups, by far the largest target audience of Falcon’s customers. Due to this ongoing trend, we see a continued growth in demand for large warehouses.
Also, post GST implementation, companies have started to look at warehouses from an efficiency perspective rather than a tax optimization perspective. This has also resulted in consolidation of small warehouses into bigger ones which are ready for large-scale automation.
We are also seeing a slew of big players coming up with large Industrial/Logistics parks in different corners of the country. These establishments offer high quality infrastructure to companies that was largely missing till a few years ago.
Automation success stories are no longer a scarce commodity. Several companies have experienced the benefits of automation in the last decade. This has brought about a mindset change across the industry, and many more companies are now feeling confident about investing in Warehouse Automation. Overall, the warehouse automation market in India is ripe for explosion in over a decade.
Tell us about your inter-logistics warehouse automation systems, and what are the main technologies deployed for it?
Falcon today has 4 core Product Lines-
Sortation Systems– These are high tech industrial machines that are deployed to sort a wide variety of items based on a set of pre-defined business rules. At Falcon, we have developed a wide range of Sortation technologies that are capable of handling up to 40,000 sorts per hour and are some of the fastest systems globally.
Conveyor Automation Systems– Efficient goods movement is the backbone of any modern-day warehouse and we offer one of the widest range of conveying technologies that can be deployed in a complex environments. While there are a lot of companies manufacturing conveyors, very few companies have the ability to delivery really large scale and complex conveyor projects.
Pick/Put To Light Systems– Falcon offers its indigenously developed range of Pick/Put to Light Systems that can deployed for multiple uses cases such as- Order Consolidation, Order Picking, Kitting, Guided Put Away and Sorting. These are simple yet effective Light Guided Assistance systems to warehouse workers that helps them by guiding the actions through a seamless symphony of Software and Light Units.
DWS Systems– We also specializes in Static and Dynamic Dimension and Weight Scanning Systems that can capture the Barcode, Weight, Dimension and Image of an Object automatically. This data can be relayed in real time to Client’s WMS/ERP systems which then can be used for a host of use cases such as- Freight Calculation, Storage Space Optimization, Packaging Size recommendation, Truck Load Optimization etc.
Furthermore, we are also going to introduce our new 3D Robotic Shuttle Technology – Neo3D – in 2022 that will transform the way companies perform order picking/ consolidation.
What are some of the main challenges that your clients often encounter, and how do you overcome them?
Most of our clients struggle with shortage of skilled manpower, unavailability of robust warehouse buildings and unpredictable volume surge.
While there is very little that Falcon can do to solve real estate related issues, but we have definitely been able to help our clients in solving manpower and volume surge related challenges.
Like I mentioned earlier, our systems can be operated with a very limited headcount and still churn out the same processing volumes as compared to a completely manual setup. These systems are really easy to use. Within minutes an operator can get trained and start working. This is the biggest pain-point that we have been able to solve for our clients.
Our systems are quite modular, and it’s really easy to scale up and scale down the production capacities at different times of the year depending on the volume surge. This prepares our clients to tackle seasonality related challenges quite efficiently.
Note: This Interview By Aditya Chaturvedi, Associate Editor at Geospatial World was Originally Published in www.geospatialworld.net, 01/27/2022